Damping in Dense Gas Acoustic Structure Interaction
Large centrifugal compressors, which are commonly applied in the oil and gas and in the process industry, may fail due to vibrations of the impeller. These vibrations are induced by pressure pulsations in a compressor stage. These vibrations can be especially strong in so-called dense gas compressors due to the strong coupling between gas and structure. Dense gas compressors are for instance applied to compress carbon dioxide to pressures up to 200 bar. In these compressors coupling between the high density fluid and the impeller structure may occur, a phenomenon called Fluid Structure Interaction (FSI). Extremely large pulsations are generated when a coupled acoustic/structural resonance mode is hit. This can happen at the impeller blade passing frequency and multiples of this frequency.
In a Joint Industry Project (JIP) the occurrence of coupled resonance modes has been investigated using models and experiments. The results of this project show that FSI has a large effect on the vibration modes of the impeller. With a COMSOL Multiphysics® model of a compressor stage, including the Structural Mechanics Module and the Acoustics Module, the coupled eigenfrequencies and modes are calculated. The calculated and measured mode frequencies agree with satisfactory accuracy. However, the predicted damping of the coupled modes showed large discrepancies with our experiments. It is suspected that the models used for damping are not adequate. To improve the damping models, future research is necessary in which new methods will be developed.
In this paper the currently used models and their validation are presented. Furthermore, modeling of damping and possible improvements are discussed.
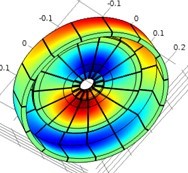
Herunterladen
- smeulers_paper.pdf - 1.27MB
- smeulers_abstract.pdf - 0.09MB