Design and Analysis of a Hyperelastic Pneumatic Honeycomb Network Made of Ecoflex 00-35
Soft robotics allows for an increased flexibility and adaptability in the field of robotics, for example increased safety with regard to human-machine systems [1]. The Pneumatic Honeycomb Network (PHN) analyzed in this paper is a constitutive element in a new approach of dynamically sealing components. Fig. 1 shows an example of such a PHN. Shape and volume of this biology-inspired hyperelastic polymer structures can be changed by applying pneumatic pressure. Utilizing COMSOL Multiphysics®, this work focuses on the behavior analysis of the PHN. The expansion properties and the contact behavior are investigated.
The COMSOL Multiphysics® model setup is based on the 2D Solid Mechanics interface. An example of a considered PHN chamber geometry is shown in Fig. 2. A Hyperelastic Material domain node is used to enable the five parameter Mooney-Rivlin material model for the PHN polymer. The stiff outer layer of the PHN is approximated by a Fixed Constraint boundary condition. Three Boundary Load conditions, configured with load type Pressure, are utilized to apply pneumatic load to various soft PHN chambers. The pressure values are parameterized to allow for load ramping in the Study by using an Auxiliary Sweep. This significantly improves the convergence of the contact simulation. A Contact Pair boundary condition in Penalty formulation is used to model the landing of the PHN-chambers on a rigid surface. A simulation result is shown in Fig. 3. Based on a Parametric Sweep the impact of geometry parameters is investigated. More details about the model setup including mesh generation are described in the paper.
For realistic material behavior, uniaxial tensile tests are performed to characterize the elastic material Ecoflex 00 35 [2]. The tensile tests are carried out according to DIN 53504. Based on the obtained stress-strain data, the Mooney-Rivlin model parameters C01 to C20 are extracted for each material. The required curve fitting is performed with a dedicated MatLab script [3]. More details regarding material parameters are reported in the paper. For model validation, a PHN prototype is realized. The prototype is operated with varied pressure and the resulting expansion is measured as shown in Fig. 4. The experimental data is found in good consistency with the simulation results.
The developed COMSOL Multiphysics® model yields the fundamental relationship between maximum elongation of a PHN and its geometric quantities length and thickness. With the model it is possible to create a PHN that uses minimal amounts of material while achieving high expansions with minimal load. This makes the future design process of a PHN much more target-oriented.
References
[1] D. Trivedi, C. D. Rahn, W. M. Kier, & I. D. Walker: Soft robotics: Biological inspiration, state of
the art, and future research. Applied Bionics and Biomechanics, 5(3), 99-117, 2008.
[2] KauPo Plankenhorn e.K. ECOFLEX® 00-35. [Online]. Available: https://www.kaupo.de/shop/out/media/ECOFLEX_0035.pdf. Accessed Mai 26, 2020.
[3] N. Philippin, A. Schreivogel, I. Kuehne & J. Kostelnik: Electronics of a new dimension - Potentials of stretchable foil systems for development of interactive microimplants. EBL - Elektronische Baugruppen und Leiterplatten, Fellbach, 68-73, 2020.
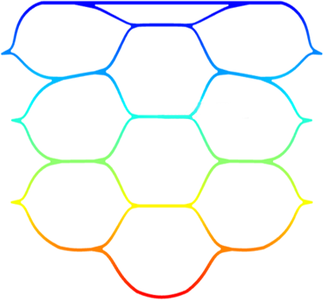