Design and Simulation of 3D Printed Check Valves Using Fluid-Structure Interaction
Passive, one-way valves, also known as check valves, while common at the macro scale, are an essential microfluidic feature that facilitate flow rectification. These structures are also commonly used in reciprocating micropump configurations to control flow. Their operation can be compared to a traditional diode in electronics, in that current is allowed to flow in only one direction (analogous to volumetric flow), but only after a small forward voltage is applied (analogous to pressure). Check valves are often rated by the cracking pressure of the check valves, which is the minimum (upstream or forward) pressure required to open the valve and allow flow. In microfluidics, numerous examples of check valves have been demonstrated, particularly in soft-lithography techniques that use PDMS, taking advantage of its extremely low Young’s modulus (E ~ 1 MPa). The purpose of this study was to use the fluid-structure interaction (FSI) module to analyze flexible materials commonly used in FDM 3D printers (Figure 1) for possible use in a microfluidic system to separate particles by size and deliver precisely controlled volume droplets. The FSI MEMS module was adapted to describe the moving mesh associated with check valve geometries between 1 and 10 μm in width, extending 46 μm out into a 100 μm wide channel. Preliminary results indicate that a material with a sufficiently low Young’s Modulus, such as thermoplastic polyurethane (TPU) (E = 4.5 MPa), is required for the relatively low flow rates found in microfluidic channels to adequately actuate the valve and promote forward flow. At a mean inlet flow rate of 40 µm/s, TPU (wall thickness = 3 μm, length = 46 μm) was shown to deform approximately 13.6 μm from perpendicular to the original flow stream (displacement of approximately 9.3 μm are needed to allow flow for TPU valves). Other 3D printer filaments (PLA, ABS, nylon and PETG) that have much larger Young’s Modulus were shown to deform only under much higher flow rates that are not practical for microfluidics (v > 70 μm/s). Future studies will allow us to optimize check valve geometry related to realizable 3D printed features, and also determine the minimum flow rates required to open the check valves for a variety of designs including interdigitated arrays of the valves and custom geometric shapes to enhance the effectiveness of the structures to prevent backflow.
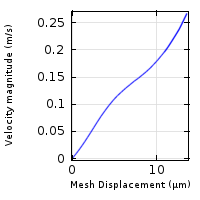
Herunterladen
- melvin_poster.pdf - 2.74MB
- melvin_paper.pdf - 0.92MB
- melvin_abstract.pdf - 0.03MB