Simulation of Thermal Breakdown in a Multi-Layered Stack of Dielectric Elastomers
Dielectric elastomers are a promising group of smart materials, which finds application within many fields such as soft robotics, wave-energy harvesting, and loud speakers. A dielectric elastomer consists of a thin, stretchable polymer film sandwiched between two compliant electrodes. When an external voltage is applied to the electrodes, an electrostatic pressure across the elastomer is generated, which will cause the electrodes to attract one another. Thereby the thickness of the elastomer is decreased and the cross sectional area of the elastomer is increased. When the voltage is switched off, the elastomer restores its original shape. Dielectric elastomers are highly flexible, thus they can be configured in many different ways, depending on the desired application, driving force, and operating strain. By stacking dielectric elastomers on top of each other, such that elastomer and electrode layers alternate, it is possible to increase the obtainable mechanical force.
Several aging mechanisms are prone to occur during operation of dielectric elastomers. One of the most significant aging mechanisms is thermal breakdown, which occurs due to build-up of heat within dielectric elastomer. Heat is generated mainly through Joule heating, and if the heat generated exceeds the heat loss at the surface of the stack, the temperature will increase exponentially and a thermal breakdown is likely to occur. The frequency of thermal breakdown increases significantly when stacking multiple layers of dielectric elastomers.
In this work the COMSOL Multiphysics® software is used to obtain a better understanding of thermal breakdown in a cylindrical stack of multiple dielectric elastomers. A 2D axisymmetric model is set up in COMSOL Multiphysics® by using the “Solid Mechanics” module, “Electrostatics” module, and the “Electromechanical Forces” Multiphysics coupling to model the deformation of the stack, and using the “Electric Currents” module, “Heat Transfer in Solids” module, and “Electromagnetic Heating” Multiphysics coupling to model the joule heating within the stack. Different heat transfer functions are applied to the surface of the stack, to see the effect of these on the point of thermal breakdown. The material of interest for the elastomer is crosslinked polydimethylsiloxanes, which is modelled using experimentally determined material parameters and using the Yeoh model as the hyperelastic material model.
The point of thermal breakdown in a stack of dielectric elastomers was studied by varying the material parameters, heat transfer functions, as well as the applied voltage and number of layers in the stack. Furthermore, it is also studied how having passive areas in the stack of dielectric elastomers effect the point of thermal breakdown.
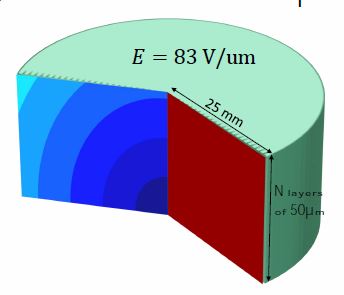
Herunterladen
- madsen_presentation.pdf - 1.56MB
- madsen_poster.pdf - 1.44MB
- madsen_abstract.pdf - 0.07MB