Buckling of a Composite Cylinder
Application ID: 67261
Buckling is a structural instability that can lead to failure of a component even without initial material failure. Computation of the critical buckling loads and mode shapes can therefore be important from a design viewpoint, even though it has previously been determined that the loading of the component only causes elastic deformations. This applies to components made from laminated composite materials, where elastic properties, ply thicknesses and stacking sequence of a composite laminate will affect buckling loads and mode shapes.
This example illustrates a linear buckling analysis of a composite cylinder under compressive loading and fixed-end conditions. The composite cylinder is made up of eight layers (plies) of a carbon fiber reinforced polymer (CFRP) material having different fiber orientations. An Equivalent Single Layer (ESL) theory based approach is used for this analysis. The effect of stacking sequence on the critical load factor is analyzed for different types of balanced laminates, such as a symmetric angle-ply laminate and an antisymmetric angle-ply laminate.
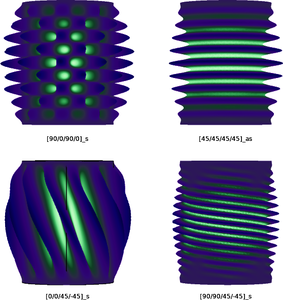
Dieses Beispiel veranschaulicht Anwendungen diesen Typs, die mit den folgenden Produkten erstellt wurden:
Allerdings können zusätzliche Produkte erforderlich sein, um es vollständig zu definieren und zu modellieren. Weiterhin kann dieses Beispiel auch mit Komponenten aus den folgenden Produktkombinationen definiert und modelliert werden:
Die Kombination von COMSOL® Produkten, die für die Modellierung Ihrer Anwendung erforderlich ist, hängt von verschiedenen Faktoren ab und kann Randbedingungen, Materialeigenschaften, Physik-Interfaces und Bauteilbibliotheken umfassen. Bestimmte Funktionen können von mehreren Produkten gemeinsam genutzt werden. Um die richtige Produktkombination für Ihre Modellierungsanforderungen zu ermitteln, lesen Sie die Spezifikationstabelle und nutzen Sie eine kostenlose Evaluierungslizenz. Die COMSOL Vertriebs- und Support-Teams stehen Ihnen für alle Fragen zur Verfügung, die Sie diesbezüglich haben.