Cooling Study of Baffles Integration in the Molding Industry
In the molding industry, high productivity rate, low energy consumption, large 3D parts, and homogeneous temperature distribution are the main targets. The 3iTech® inductive technology developed by RocTool ensures both good temperature homogeneity and short heating time. Conventionally, to guarantee efficient cooling, a turbulent water flow is directly integrated into the mold. Ideally, to cope with the temperature homogeneity requirements for 3D shaped parts, cooling lines are expected to follow the molding surface at a constant distance. Additive manufacturing techniques which generate conformal integration are of high interest for small parts while drilling operations are still the best options for large parts. As part of drilling operations, the so called baffle geometry is particularly well suited when cooling complex geometries. The heat transfer coefficient (htc), which has been extensively studied in the literature for simple configuration such as cylindrical tube, is not defined for such complex geometries and requires specific numerical studies. In the present study, the CFD turbulent model has been developed in collaboration with SIMTEC.
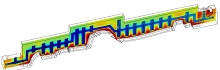
Herunterladen
- noailles_poster.pdf - 1.13MB
- noailles_abstract.pdf - 2.79MB