Extension of an electrochemical model to metal polishing
Additive manufacturing allows to design and to realize parts with complex geometries, which are difficult, even impossible, to obtain by conventional means. Nevertheless, the final surface finish obtained at the end of the 3D printing process do not fit with technological specifications especially due to high roughness levels. Thus, an additional finishing step must be implemented in order to get the expected surface finish. Electrochemical polishing is of great interest because it allows, as main advantage comparatively to tribological ones, to be able to deal with small parts exhibiting high complex shapes and/or material hard to be polished [1]. Electropolishing is an electrolytic process based on the anodic dissolution of the workpiece under constant current or potential [2]. As it is done for electroplating systems, it is nonetheless necessary to uniformize the current distribution lines in the treatment cell, in order to optimize the effect of the finishing on the whole surface of the parts. The ability to provide a relevant simulation of the processing by the help of an accurate modelling is a major issue to ensure its industrial deployment through the development of specific tools and the selection of relevant operating parameters [3]. In this objective, the use of a secondary current distribution model is a useful first step and gives interesting results if special care is paid to the specificity of electropolishing processes. However, this approach faces limitations because of the agitation into the treatment cell which is not accounted for by the model. A correction is possible by integrating the influence of an average level of agitation on the polarization curves (current vs potential) used in the simulation thanks to different electrochemical data sets. At this stage, the tertiary current distribution model has been set aside because of its complexity in the collection of specific data, which is time consuming. Then, the present work describes a model based on secondary current distribution upgraded by considering a global agitation. After comparing experimental results vs. simulations, it had been demonstrated that even if the prediction ability was significantly improved in term of dissolution rates and roughness reduction, some discrepancies still remains, confirming the need of a breakthrough in the scientific approach. From this work, two main conclusions can be drawn: the reliability of implemented data is decisive and among them, quantitative values for local agitation at the surface vicinity are also critical.
[1] C. Rotty, A. Mandroyan, M-L Doche, J-Y Hihn, Surface & Coatings Technology vol.307 p125–135 (2016). [2] P. A. JACQUET, Nature vol.135 p1076 (1935). [3] V. URLEA, V. BRAILOVSKI, Int. J. Adv. Manuf. Technol. vol.92 p4487–4499 (2017).
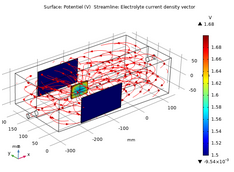