Multiphysical Optimization of the Next Generation of Energy Efficient High Temperature Furnaces
To achieve the goals of the Paris Agreement and limit global warming below 2 K compared to pre-industrial level, significant energy savings in all fields of industries will be required. One example of energy intensive processes in industrial fabrication is heat treatment. The applied high temperature vacuum furnaces are generally equipped with a fast cooling system and offer a big potential for energy savings, as they typically have operation powers of serval hundred kilowatts and process times can go up to more than 24 hours. In the development of refractory metal hotzones for high temperature vacuum furnaces at PLANSEE SE, multi-physical simulations are a tool for the identification of major sources of energy losses and the evaluation of the influence of new design concepts on the performance of the furnaces. In this contribution, thermal, thermo-electric and thermo-fluid dynamic models are applied for an optimization of high temperature vacuum furnaces with respect to energy efficiency, temperature homogeneity and fast cooling performance. A 3D transient thermo-electric model of a full high temperature vacuum furnace, based on the Heat Transfer Module and AC/DC Module of COMSOL Multiphysics®, allows an analysis of its power consumption and temperature homogeneity. It considers electric heating, heat transfer in solids, surface to surface radiation and convective cooling. Figure 1 shows the heating of a 600 kg molybdenum load in a furnace with a state of the art hotzone. For the evaluation of the cooling performance of the furnace, a 3D transient thermo-fluid dynamic model is applied. It is based on the Heat Transfer Module and CFD Module and considers heat transfer in gas and solids, turbulent fluid flow, surface to surface radiation and convective cooling. Figure 2 shows the cooling of a 600 kg molybdenum load. The results on power consumption, temperature homogeneity and cooling rate obtained from the multi-physical models show good correlation to experimental data obtained at a test furnace at PLANSEE SE. In a next step, based on the previously described models new design concepts for gas inlets and outlets with an improved shielding efficiency for thermal radiation and an unchanged low resistance for the cooling gas flow are evaluated with respect to power consumption, temperature homogeneity and cooling efficiency. Figure 3 shows a stationary thermal simulation of a high temperature furnace with a new, compact concept for the rear gas oulet leading to a reduced power consumption and an improved temperature homogeneity. In order to reduce the energy losses through the gas inlet nozzles, based on a thermo-fluid dynamic simulation design concepts for additively manufactured inserts with a high shielding efficiency and a low flow resistance were evaluated (see Figure 4). The developed concepts for gas inlets and outlets were implemented and tested at the test furnace at Plansee SE and energy savings of 14 % could be demonstrated, at a significantly improved temperature homogeneity and a comparable cooling performance. The presented developments are included in the next generation of energy efficient PLANSEE refractory metal hotzones for high temperature vacuum furnaces.
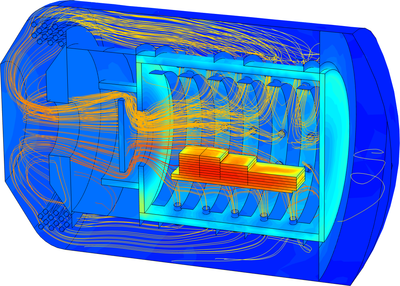