Multiphysics Simulation of the Effect of Sensing and Spacer Layers on SAW Velocity
Surface acoustic wave gas sensors use a chemically sensitive resistive layer to detect gas concentration. The resistivity of the sensing material, the sensing layer thickness, and the spacer layer thickness all affect the surface wave propagation velocity. Existing analytic theory relates the change in velocity to various parameters. However some variables in this theory are not unambiguously defined. Accurate simulations require inclusion of electrostatic effect and acoustic wave propagation in the sensing layer and spacer layer. In this paper we performed simulation of surface acoustic wave propagation in layered structure using multiphysics finite element package COMSOL 3.4a and 3.5, 2D piezo plane strain mode. The effect of thickness and materials of sensing and spacer layer are analyzed to optimize SAW gas sensor design.
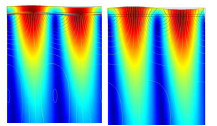
Herunterladen
- Zheng_pres.pdf - 0.42MB
- Zheng.pdf - 0.21MB