Noise and Vibration Simulation of a Vacuum Cleaner Robot Gearbox
A gearbox used in a vacuum cleaner robot is evaluated regarding noise and vibration in COMSOL Multiphysics®, using the Multibody Dynamics and the Acoustics Module. The real gearbox is powered by a DC motor and consists of four plastic helical gears forming a gear train and is used to rotate a brush that cleans the floor. For modelling the gearbox vibration, the Multibody Dynamics Module is used. In a first step, the gear mesh stiffness is determined for each gear pair by performing stationary, parametric contact analyses. Based on these results, the gearbox multibody model is built up for the gear train using the gear pair joint including gear elasticity (mesh stiffness), backlash and transmission error. The gearbox casings are simulated as flexible domains, so the vibrations caused by the gear can spread out. The time-dependent study is run for one complete revolution of the output gear shaft. As a result, the normal acceleration over frequency can be evaluated in different locations on the gearbox casing surfaces. After transforming the multibody dynamics model output from time- to frequency-domain by FFT, the normal acceleration of the gearbox surfaces is the input for the acoustics model and gets used as the sound source. A half sphere solid filled with air surrounds the gearbox and simulates the space where the acoustical waves propagate. The parametric study is performed in a wide range of hearable frequencies from 100 Hz to 5000 Hz. For verification of the simulation model, an acoustic measurement is performed, using the same gearbox working point as the multibody dynamics simulation. The operational sound pressure level (SPL) of the gearbox is measured in different microphone locations and compared to the simulation results to determine the overall quality of the simulation model.
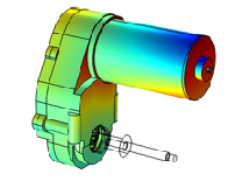