Acoustic Streaming Driven Mixing
Introduction - The ability to achieve rapid and homogeneous mixing at microscales is one of the essential requirements for various lab-on-a-chip applications [1]. The flow at microscales is characterized by low Reynolds number, resulting in laminar flow patterns. Thus, the mixing at microscales is dominated by slow diffusion process. Recently, an rapid and homogeneous mixing was demonstrated using an oscillating sharp-edge based acoustic micromixer which utilized the phenomenon of the nonlinear interaction of acoustic waves with fluid, resulting in fluid motion called as acoustic streaming [2],[3]. Fig.1 shows the schematic of the sharp-edge-based acoustofluidic micromixer consisting of a single-layer polydimethylsiloxane (PDMS) channel with sharp edges on its sidewall and bonded onto a glass slide. Upon the excitation of acoustic waves via a piezoelectric transducer, the sharp edges are oscillated, resulting in acoustic streaming. This acoustic streaming motion of the fluid was used to mix two different incoming streams of fluids to achieve rapid and homogeneous mixing.
In this work, we present a finite element model created in COMSOL Multiphysics® software to numerically study the mixing phenomenon in acoustically oscillating sharp-edge based micromixer by solving Navier-Stokes equations in conjunction with the convection-diffusion equation. These equations were solved successively using the Weak Form PDE interface along with the Transport of Diluted Species interface.
Use of COMSOL Multiphysics - We model the fluid motion using the compressible Navier-Stokes equations and the concentration profile using the convection-diffusion equation. To circumvent the numerical challenges associated with obtaining a direct solution of these equations [3], we utilize a perturbation approach to compute acoustic streaming flow along with the convection-diffusion equation to investigate the mixing, resulting in governing equations shown in Fig. 2. The flow equations are solved first to calculate the mean Lagrangian velocity, vL (which can be calculated using v1 and v2) which is then used to solve the concentration-diffusion equation.
Results - Figure 3 shows the numerical results for (a) the laminar flow pattern in the absence of acoustic streaming, (b) the acoustically perturbed flow patterns in the presence of acoustic actuation, and (c) the concentration profile inside the acoustically oscillated sharp-edge based micromixer. The numerical model was also qualitatively validated using the experimental results. Further results on the design and operational optimization of the sharp-edge based micromixer will be presented and some strategies for improving the performance will be discussed using our numerical model.
Conclusion - In conclusion, we presented a numerical model for investigating acoustic mixing inside a sharp-edge based micromixer. We believe that our computational model, while providing a better understanding of the mixing phenomena inside sharp-edge-based micromixers, would be useful in setting the design criteria as well as the geometrical and operational optimization of several other sharp-edge-based lab-on-a-chip applications.
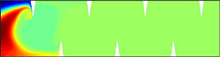
Herunterladen
- nama_presentation.pdf - 2.36MB
- nama_abstract.pdf - 0.31MB