Gezeigt werden Events mit Startzeiten zwischen: 08:00 – 20:00
Suchen
Bevorstehende Events
Lade Events
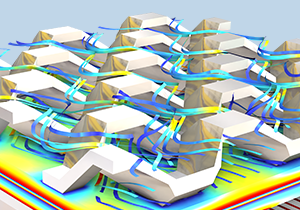
Juli 22
| 14:00 CEST
Solving Large Models in COMSOL Multiphysics®
COMSOL
Webinar
Online
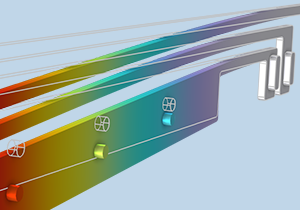
Juli 22–25
| 17:00 EDT
Introduction to COMSOL Multiphysics®
COMSOL
Trainingskurs
Online

Juli 22
| 20:00 EDT
Modeling Next-Generation Battery Technologies with COMSOL Multiphysics®
Battery Technology
Webinar
Online

Juli 24
| 20:00 EDT
Digital Twin Modeling of Human Thorax for HFCC Therapy Using COMSOL Multiphysics®
IEEE
Webinar
Online
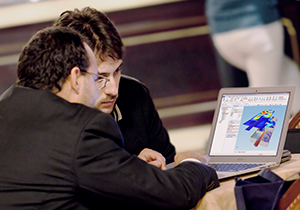
Juli 28–29
| 09:00 CEST
COMSOL Multiphysics® Intensive Training (2 Days)
COMSOL
Trainingskurs
Zoetermeer

Juli 29
| 20:00 EDT
Multiphysics Modeling of Power Electronics
COMSOL
Webinar
Online
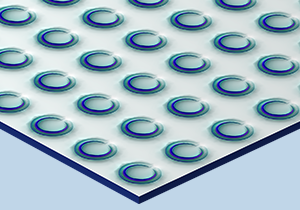
Juli 31
| 15:00 BST
Modeling Acoustic Metamaterials in COMSOL Multiphysics
COMSOL
Webinar
Online

Aug. 5–7
| 10:30 BST
Introduction to COMSOL Multiphysics®
COMSOL
Trainingskurs
Online
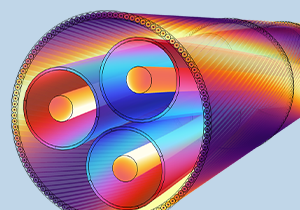
Aug. 5
| 14:00 CEST
Simulating Electrical Power Systems for the Grid
COMSOL
Webinar
Online
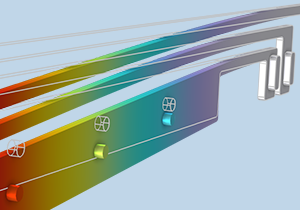
Aug. 5
| 17:30 EDT
The Basics of COMSOL Multiphysics® in 18 Minutes
COMSOL
Webinar
Online

Aug. 7
| 20:00 EDT
Moisture Transport Modeling in COMSOL Multiphysics®
COMSOL
Webinar
Online
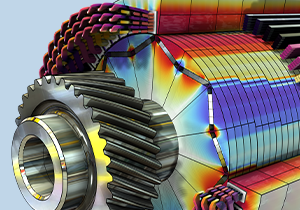
Aug. 14
| 15:00 BST
Modeling and Simulation for Electric Motor Design
COMSOL
Webinar
Online
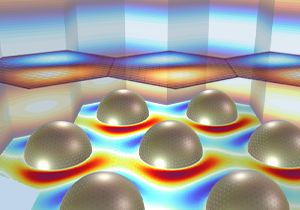
Aug. 14
| 20:00 EDT
Modeling Periodic Structures in RF and Optics
Physics Today
Webinar
Online

Aug. 18–25
| 11:00 IST
Training Course: Modeling Plasma in COMSOL Multiphysics®
COMSOL
Trainingskurs
Online
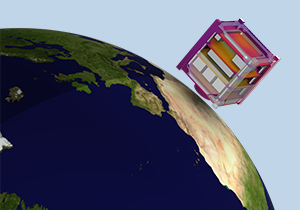
Aug. 19
| 14:00 CEST
Analyzing Spacecraft Thermal Performance
COMSOL
Webinar
Online

Aug. 19
| 20:00 EDT
Modeling Room Acoustics in COMSOL Multiphysics®
COMSOL
Webinar
Online

Aug. 26–29
| 17:00 EDT
AC/DC Modeling in COMSOL Multiphysics®
COMSOL
Trainingskurs
Online

Aug. 28
| 15:00 BST
Prediction of Electromagnetic Signatures of Naval Vessels with COMSOL Multiphysics
COMSOL
Webinar
Online

Sept. 2–4
| 10:30 BST
Introduction to COMSOL Multiphysics®
COMSOL
Trainingskurs
Online

Sept. 2
| 14:00 CEST
Design Optimization for Engineering Problems
COMSOL
Webinar
Online

Sept. 3
| 15:00 BST
Optimization of Thermal Management Systems
COMSOL
Webinar
Online
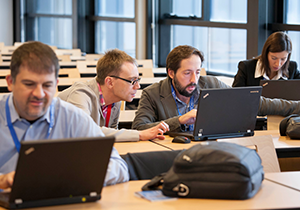
Sept. 8–9
| 09:00 CEST
On-site: Heat Transfer Intensive Training Course (2 Days) - Zurich
COMSOL
Trainingskurs
Zurich
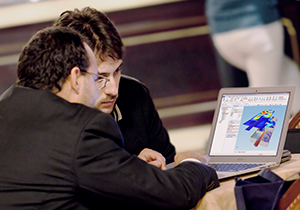
Sept. 9
| 08:00 EEST
COMSOL Multiphysics Open Training
COMSOL
Training
Espoo
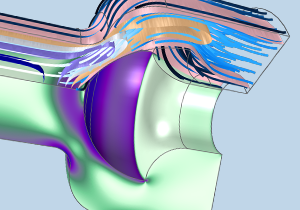
Sept. 9–12
| 17:00 EDT
CFD Modeling in COMSOL Multiphysics®
COMSOL
Trainingskurs
Online
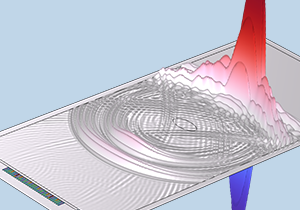
Sept. 9
| 20:00 EDT
Modeling Ultrasound Acoustics for Biomedical Applications
COMSOL
Webinar
Online
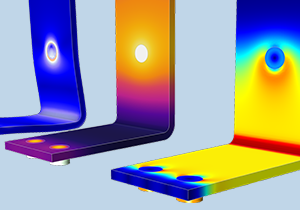
Sept. 15–18
| 09:00 CEST
Modellierung mit COMSOL Multiphysics® (Online)
COMSOL
Trainingskurs
Online
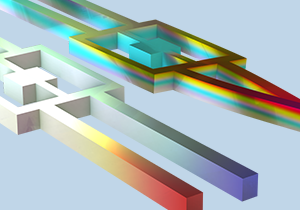
Sept. 16–19
| 17:00 EDT
Structural Mechanics Modeling in COMSOL Multiphysics®
COMSOL
Trainingskurs
Online
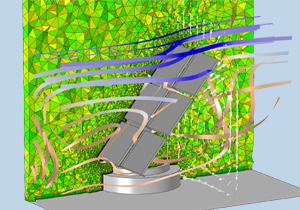
Sept. 22–25
| 09:00 CEST
Fortgeschrittene Modellierung mit COMSOL Multiphysics® (Online)
COMSOL
Trainingskurs
Online

Sept. 23
| 13:00 CEST
COMSOL & Coffee: Göttingen
COMSOL
Workshop
Göttingen
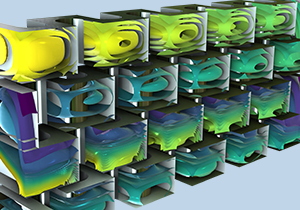
Sept. 23
| 14:00 CEST
Process Engineering: Fluid Flow & Chemical Reactions
COMSOL
Webinar
Online
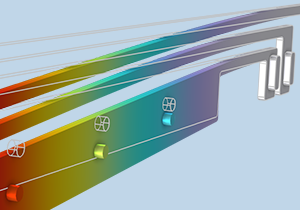
Sept. 23–26
| 17:00 EDT
Introduction to COMSOL Multiphysics®
COMSOL
Trainingskurs
Online

Sept. 23
| 20:00 EDT
Modeling and Simulation of MEMS Devices
COMSOL
Webinar
Online
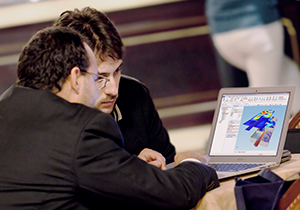
Sept. 24
| 08:30 EEST
Open Training: Introduction to modern simulation workflow
COMSOL
Training
Tampere
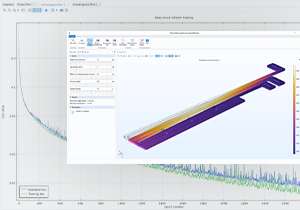
Sept. 25
| 09:30 CEST
COMSOL Modeling Seminar at EPFL
COMSOL
Workshop
Lausanne
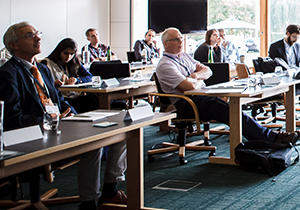
Sept. 29–30
| 09:00 CEST
COMSOL Multiphysics® Intensive Training (2 Days)
COMSOL
Trainingskurs
Zoetermeer
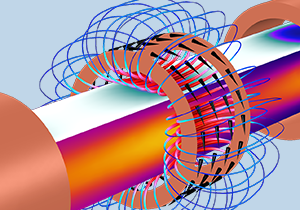
Okt. 6–9
| 09:00 CEST
AC/DC-Modellierung (Online)
COMSOL
Trainingskurs
Online
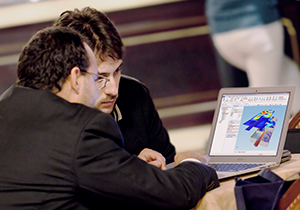
Okt. 7–8
| 08:30 CEST
(In-person) COMSOL Multiphysics® Intensive Training Course (2 Days)
COMSOL
Trainingskurs
Kgs. Lyngby
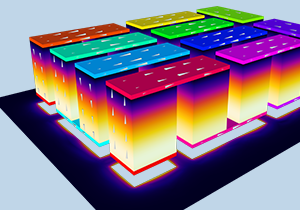
Okt. 7
| 14:00 CEST
Equation-Based Modeling with COMSOL®
COMSOL
Webinar
Online
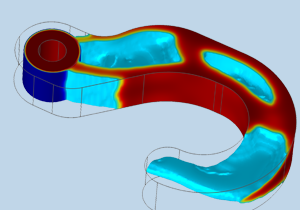
Okt. 9
| 14:00 CEST
Optimierung keramischer 3D-Drucke durch Simulation
COMSOL
Webinar
Online
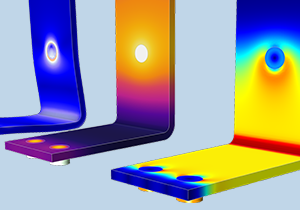
Okt. 13–16
| 09:00 CEST
Modellierung mit COMSOL Multiphysics® (Online)
COMSOL
Trainingskurs
Online
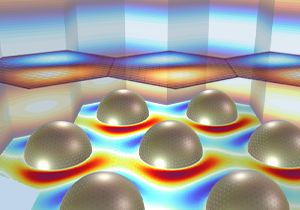
Okt. 14
| 14:00 CEST
Wave & Ray Optics Modeling with COMSOL®
COMSOL
Webinar
Online
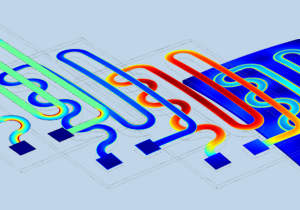
Okt. 14–17
| 17:00 EDT
Heat Transfer Modeling in COMSOL Multiphysics®
COMSOL
Trainingskurs
Online
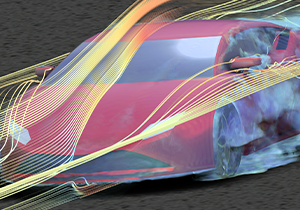
Okt. 20
| 08:30 CEST
COMSOL Modeling Seminar at ETH Zurich
COMSOL
Workshop
Zürich
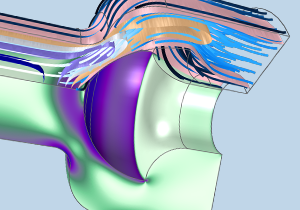
Okt. 20–21
| 09:00 CEST
CFD-Modellierung (Online)
COMSOL
Trainingskurs
Online

Okt. 21–24
| 17:00 EDT
RF Modeling in COMSOL Multiphysics®
COMSOL
Trainingskurs
Online

Okt. 22–23
| 09:00 CEST
Plasma-Modellierung (Online)
COMSOL
Trainingskurs
Online
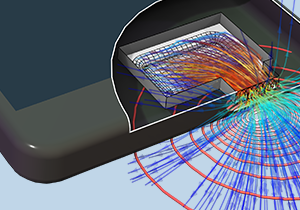
Okt. 28–31
| 16:00 EDT
Acoustics Modeling in COMSOL Multiphysics®
COMSOL
Trainingskurs
Online

Nov. 4
| 14:00 CEST
CFD Modeling with COMSOL® in 18 Minutes
COMSOL
Webinar
Online
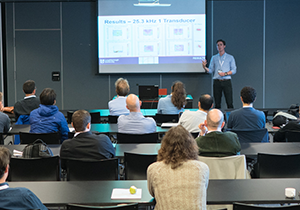
Nov. 4–5
| 15:00 EDT
Introduction to COMSOL Multiphysics®
COMSOL
Trainingskurs
Burlington
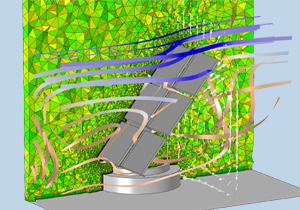
Nov. 10–13
| 09:00 CEST
Fortgeschrittene Modellierung mit COMSOL Multiphysics® (Online)
COMSOL
Trainingskurs
Online

Nov. 11–14
| 17:00 EDT
Electrochemistry & Electrodeposition Modeling in COMSOL Multiphysics®
COMSOL
Trainingskurs
Online
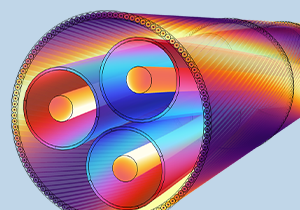
Nov. 18–20
| 09:00 CEST
Strukturmechanik-Modellierung (Online)
COMSOL
Trainingskurs
Online
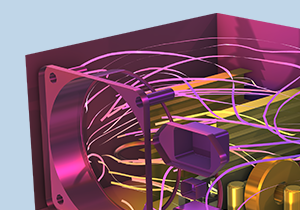
Nov. 18
| 14:00 CEST
Heat Transfer Modeling with COMSOL® in 18 Minutes
COMSOL
Webinar
Online
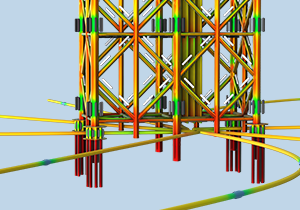
Nov. 18–20
| 17:00 EDT
Corrosion Modeling in COMSOL Multiphysics®
COMSOL
Trainingskurs
Online
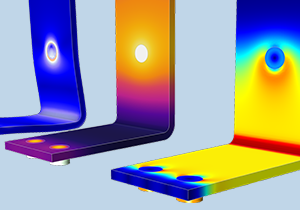
Nov. 24–27
| 09:00 CEST
Modellierung mit COMSOL Multiphysics® (Online)
COMSOL
Trainingskurs
Online
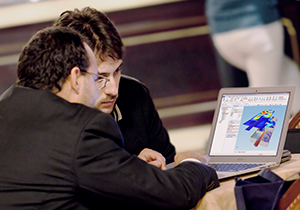
Nov. 24–25
| 09:00 CEST
COMSOL Multiphysics® Intensive Training (2 Days)
COMSOL
Trainingskurs
Zoetermeer

Dez. 1
| 09:00 CEST
Modeling Cables & Power Electronics
COMSOL
Trainingskurs
Zoetermeer
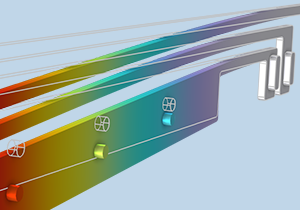
Dez. 9–12
| 17:00 EDT
Introduction to COMSOL Multiphysics®
COMSOL
Trainingskurs
Online
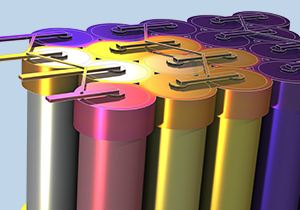
Dez. 16–19
| 17:00 EDT
Battery Modeling in COMSOL Multiphysics®
COMSOL
Trainingskurs
Online
8 von 59 Events werden angezeigt
59 von 59 Events werden angezeigt
Trainings durch Certified Consultants
Aufgezeichnete Webinare

COMSOL Day Chennai
COMSOL Day
Jul 18

Biomedical Modeling with COMSOL Multiphysics
Webinar
Jul 17
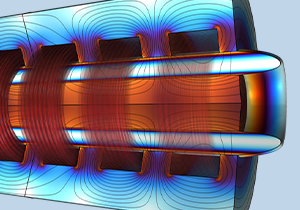
Understanding Liquid Metal Transport in Magnetic Fields — Simulating Magnetohydrodynamic Duct Flow
Webinar
Jul 11

Memristor Modeling with COMSOL Multiphysics®
Webinar
Jul 02
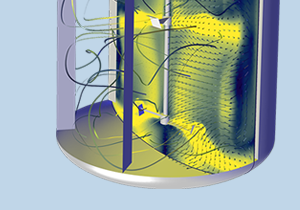
Modeling Fluid Mixers and Stirred Tank Reactors in COMSOL Multiphysics®
Webinar
Jun 26
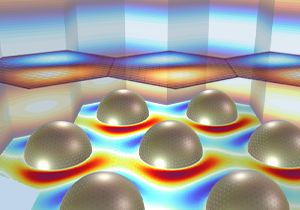
Modellierung optischer Nanostrukturen mit COMSOL Multiphysics®
Webinar
Jun 17

Underwater Acoustics
Webinar
Jun 12

Optimization in Structural Mechanics
Webinar
Jun 12
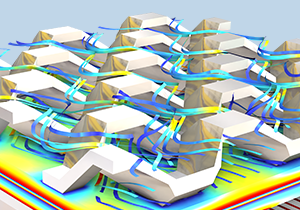
Hydrogen Technology Innovation with Simulation
Webinar
Jun 12
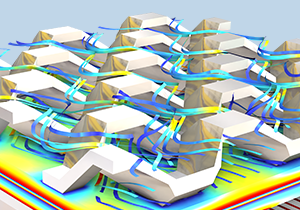
Modeling Hydrogen Fuel Cells and Electrolyzers
Webinar
Jun 12
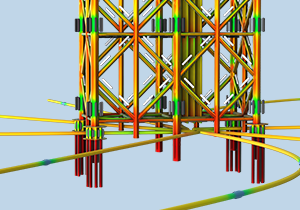
Modeling Chemical Reactions and Reacting Flows Using COMSOL Multiphysics®
Webinar
Jun 05

Introduction to Multibody Dynamics Modeling with COMSOL Multiphysics
Webinar
May 28

Automotive Acoustics Analysis Using COMSOL Multiphysics®
Webinar
May 27

Acoustics in Electronics Series, Part 4: Piezoelectric Devices
Webinar
May 20

Improving Thermal Management of Batteries with COMSOL Multiphysics®
Webinar
May 09

Demokratisierung der Multiphysik-Simulation
Webinar
May 08

Acoustics in Electronics Series, Part 3: Hearing Aids
Webinar
May 06

Acoustics in Electronics Webinar Series, Part 2: MEMS Speakers and Microphones
Webinar
Apr 16

The Basics of COMSOL Multiphysics® in 18 Minutes
Webinar
Apr 15

Optimization in RF and Wave Optics
Webinar
Apr 09

Wave & Ray Optics Modeling with COMSOL®
Webinar
Apr 09

Meshing Your Models in COMSOL Multiphysics®
Webinar
Apr 08

Multiphysics Simulation in Semiconductor Packaging
Webinar
Apr 03

Acoustics in Electronics Webinar Series, Part 1: Loudspeakers
Webinar
Mar 25
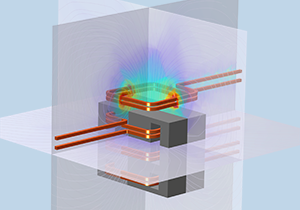
Simulating Electrical Power Systems for the Grid
Webinar
Mar 20
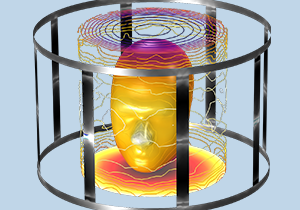
Modellierung biomedizinischer Geräte mit COMSOL Multiphysics®
Webinar
Mar 20
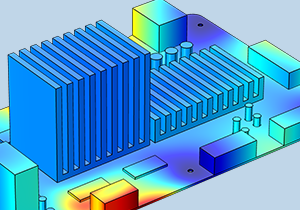
Multiphysics Modeling of Electronic Components
Webinar
Mar 20

Using Geometry Modeling Tools in COMSOL Multiphysics®
Webinar
Mar 18

Improving Thermal Management of Batteries with COMSOL Multiphysics®
Webinar
Mar 18

Modeling Chemical Reactions and Reacting Flows Using COMSOL Multiphysics®
Webinar
Mar 06

Integrating Frequency-Dependent Data into Time-Domain Acoustics Analysis
Webinar
Feb 27
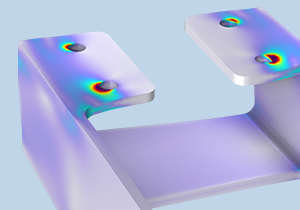
Introduction to Uncertainty Quantification
Webinar
Feb 26
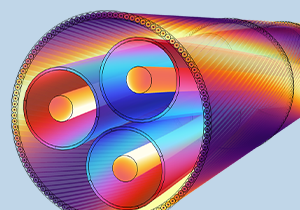
Entwicklung von Leistungselektronik und Kabelsystemen
Webinar
Feb 25

Efficient Battery Modeling with Surrogate Models
Webinar
Feb 18
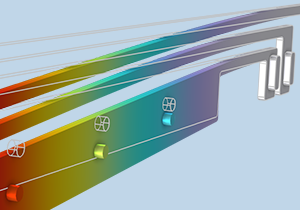
The Basics of COMSOL Multiphysics® in 18 Minutes
Webinar
Feb 13
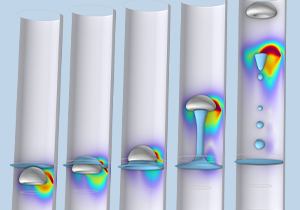
Designing a Magnetorheological-Fluid-Based Clutch Using COMSOL Multiphysics®
Webinar
Feb 13

Modeling Biochemical Sensors and Testing Devices with COMSOL®
Webinar
Jan 29
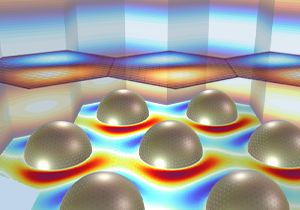
Modeling Optical Nanostructures with COMSOL Multiphysics®
Webinar
Jan 23

Electric Discharge Modeling
Webinar
Jan 21

Automotive Acoustics Analysis Using COMSOL Multiphysics®
Webinar
Jan 16
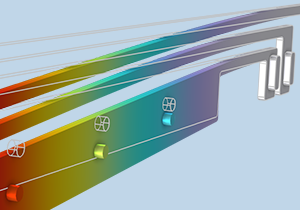
The Basics of COMSOL Multiphysics® in 18 Minutes
Webinar
Jan 14

Multiphysics Fracture Mechanics with COMSOL Multiphysics® in 18 minutes
Webinar
Dec 12

Models for Transport and Chemistry in CVD Reactors
Webinar
Dec 05

Modeling Nanophotonic Applications with COMSOL Multiphysics®
Webinar
Nov 28

Simulation für alle durch eigenständige Simulations-Apps
Webinar
Nov 27

Design Optimisation for Engineering Problems
Webinar
Nov 27
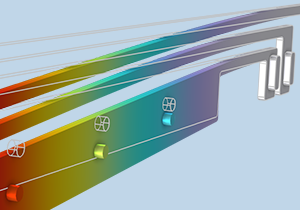
Modeling Shape Memory Alloys and Triboelectric Nanogenerators with COMSOL Multiphysics®
Webinar
Nov 21

Introducing COMSOL Multiphysics® Version 6.3
Webinar
Nov 20

Improving Thermal Management of Batteries with COMSOL Multiphysics®
Webinar
Nov 19
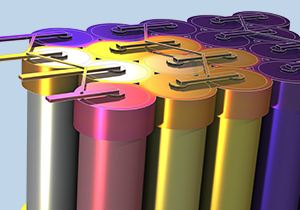
Battery Modeling with COMSOL Multiphysics®
Webinar
Nov 14
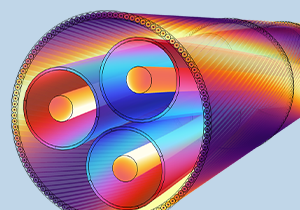
Modeling Cables & Power Electronics
Webinar
Nov 13

Improving the Manufacturing of Semiconductors with Multiphysics Simulation
Webinar
Nov 07
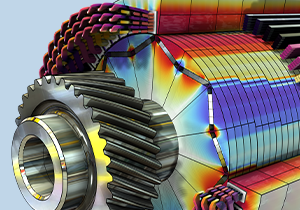
Advancements in Simulation for EV Motors
Webinar
Nov 06
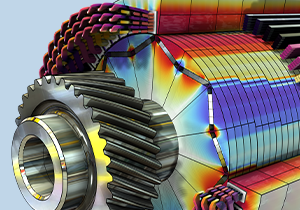
Multiphysics Modeling of Electrical Motors
Webinar
Oct 31

Modelling the Thermomechanical Behaviour of Glass Materials
Webinar
Oct 23

Fatigue and Durability Analysis using COMSOL Multiphysics®
Webinar
Oct 23
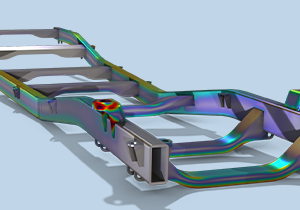
Multiphysics Modeling of Manufacturing Processes Using COMSOL®
Webinar
Oct 17

Simulating Electromagnetic Metamaterials in COMSOL Multiphysics®
Webinar
Oct 15
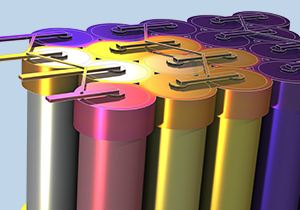
Modeling Thermal Runaway and Abuse in Batteries
Webinar
Oct 15

Simulating Electronics Packaging and Testing
Webinar
Sep 26

Electromagnetics Simulation of Printed Circuit Boards in COMSOL Multiphysics®
Webinar
Sep 26

Simulating Droplet Flow in Wearable Sweat Collection Patches
Webinar
Sep 25
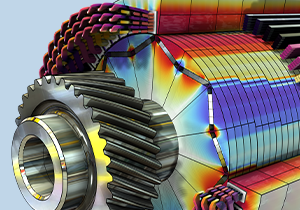
Designing Electric Motors and Drivetrains with Multiphysics Simulation
Webinar
Sep 20
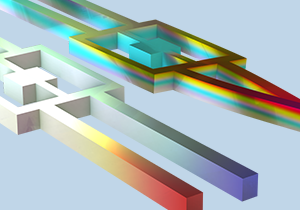
Modeling and Simulation of MEMS Devices
Webinar
Sep 19
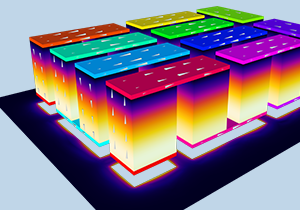
Equation-Based Modeling with COMSOL Multiphysics®
Webinar
Sep 18
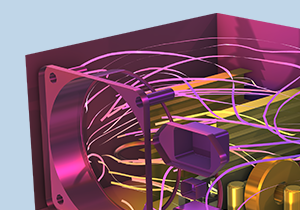
Thermal Management in Electronic Devices with COMSOL Multiphysics®
Webinar
Sep 18

Battery Modeling with COMSOL Multiphysics®
Webinar
Sep 17
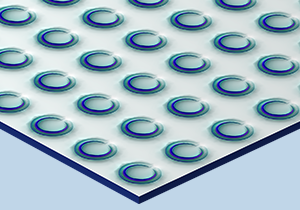
Simulating Plasmonics and Metamaterials
Webinar
Sep 12
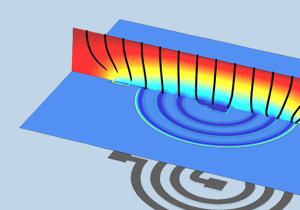
Modeling and Simulation of Electrodeposition Cells
Webinar
Aug 29
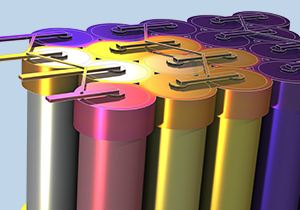
Designing Batteries with Modeling and Simulation
Webinar
Aug 28

Materialparameter abschätzen
Webinar
Aug 28

Multiphysics Modeling and Simulation for 5G Devices
Webinar
Aug 27
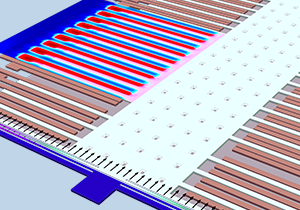
Modeling Low-Frequency Accelerometers Using COMSOL Multiphysics®
Webinar
Aug 22
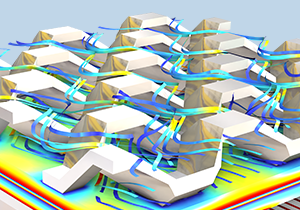
Modeling Hydrogen Production, Storage and Utilization
Webinar
Aug 21
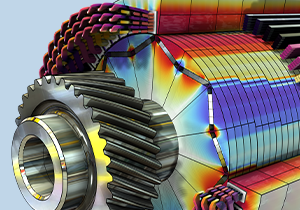
Modeling Electric Motors and Drivetrains
Webinar
Aug 20

Phased Array Antenna Modeling with COMSOL Multiphysics®
Webinar
Aug 13
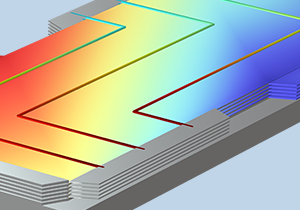
Virtual Hydrogen Lab: Computational Predictions of Hydrogen Uptake, Diffusion, and Embrittlement
Webinar
Aug 08

Modeling Fluid-Structure Interaction with COMSOL Multiphysics®
Webinar
Jul 30

Multiphysics Simulation to Improve Design of Renewable Energy Production
Webinar
Jul 25
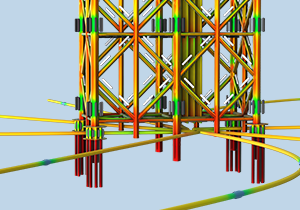
Multiphysics Simulation for Oil & Gas Processing
Webinar
Jul 19

Modeling Hydrogels and Swollen Elastomers in COMSOL Multiphysics®
Webinar
Jul 18
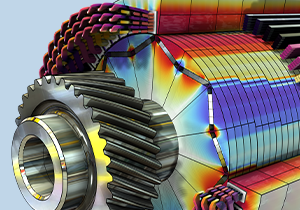
Improving Electric Drivetrain Efficiency with Multiphysics Simulation
Webinar
Dec 15
6 von 82 Events werden angezeigt
82 von 82 Events werden angezeigt
- Produktinformationen
- Produkte
- Spezifikationstabelle
- Lizenzoptionen
- Systemanforderungen
- Release-Historie
- Support und Service
- Support Center
- Meine Supportfälle
- Knowledge Base
- Partner und Consultants
- Dokumentation
- Produkt Download
- Unternehmen
- Über COMSOL
- Karriere
- Presse
- Kontakt
- |
- Datenschutzerklärung
- |
- Warenzeichen
- |
- Cookie Settings
- © 2025 by COMSOL. Alle Rechte vorbehalten