Dissociation in a Tubular Reactor
Application ID: 221
Tubular reactors are often used in continuous large-scale production, for example in the petroleum industry. One key design parameter is the conversion, or the amount of reactant that reacts to form the desired product. In order to achieve high conversion, process engineers optimize the reactor design: its length, width and heating system. An accurate reactor model is a very useful tool, both at the design stage and in tuning an existing reactor.
This example deals with a gas-phase dissociation process, where species A reacts to form B. The model illustrates the use of several attractive features in the Chemical Reaction Engineering Module:
- The use of the Transport of Concentrated Species to account for multicomponent diffusion.
- How to couple the variable density to a Laminar Flow interface.
- Implementation of temperature- and composition-dependent reaction kinetics.
- The use of a mapped mesh, which is structured, to discretize a long and thin geometry, typical for tubular reactors
- How to include heat balances and how to couple these to both the mass balances and the velocity field
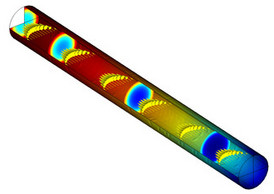
Dieses Beispiel veranschaulicht Anwendungen diesen Typs, die mit den folgenden Produkten erstellt wurden:
Allerdings können zusätzliche Produkte erforderlich sein, um es vollständig zu definieren und zu modellieren. Weiterhin kann dieses Beispiel auch mit Komponenten aus den folgenden Produktkombinationen definiert und modelliert werden:
- COMSOL Multiphysics® und
- entweder Battery Design Module, Chemical Reaction Engineering Module, oder Fuel Cell & Electrolyzer Module
Die Kombination von COMSOL® Produkten, die für die Modellierung Ihrer Anwendung erforderlich ist, hängt von verschiedenen Faktoren ab und kann Randbedingungen, Materialeigenschaften, Physik-Interfaces und Bauteilbibliotheken umfassen. Bestimmte Funktionen können von mehreren Produkten gemeinsam genutzt werden. Um die richtige Produktkombination für Ihre Modellierungsanforderungen zu ermitteln, lesen Sie die Spezifikationstabelle und nutzen Sie eine kostenlose Evaluierungslizenz. Die COMSOL Vertriebs- und Support-Teams stehen Ihnen für alle Fragen zur Verfügung, die Sie diesbezüglich haben.